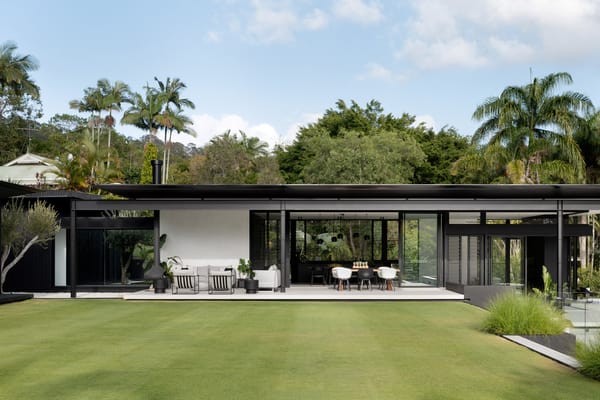
Windows & Doors
Blackwood Doonan: An Award-Winning Home by Sarah Waller
A Showcase of Design and Craftsmanship
Windows & Doors
A Showcase of Design and Craftsmanship
Facade Solutions
The Southgate Corporate Park project required meticulous attention to detail throughout every stage. One of the key challenges involved integrating the curved glazing with the horizontal sunshades while balancing the visual differences.
Windows & Doors
The Hastings Sports Stadium, which has become a vibrant community hub, features a variety of G.James products designed to meet both the functional and aesthetic requirements of the build.